- Manual Sitrans Fm Magflo Mag 5000 Series
- Mag 5000 Flow Meter
- Manual Sitrans Fm Magflo Mag 5000 For Sale
Instructions, Sitrans f m magflo, Electromagnetic flowmeter type mag 5100 w
SITRANS F M MAGFLO® Electromagnetic flowmeters Transmitter types MAG 5000, MAG 6000 s [ ] Technical Documentation (handbooks, instructions, manuals etc.) on the complete product range SITRANS F can be found on the internet/intranet on the following links. 2018-6-19 Flow Measurement SITRANS F M Flow sensor MAG 1100 and MAG 1100 HT 3 Overview The SITRANS F M MAG 1100 is an electromagnetic flow sensor in a compact wafer design designed for flow applications in the process industry. Benefits † Sensor sizes: DN 2 to 100 (1/12” to 4”) † Compact wafer design meets EN 1092, DIN and ANSI flange standards. SITRANS F M MAGFLO - Magnetic flow meter Transmitter MAG5000 Product designation Order no. 1 A A 1 0 1 B A 0 t MAG 5000, 19 Inch Insert,IP20 / NEMA 2, Aluminium, 115-230V AC 50/60 Hz 2 C A 1 0 1 A A 0 t 2 C A 3 0 1 A A 0 t 1 A A 1 0 1 A B 0 934,00 1 A A 3 0 1 A B 0 934,00. FM/CSA class 1 Div 2 t t Communication None t t Modlous RTU/RS485. 2014-7-31 SITRANS F M MAGFLO® Electromagnetic flowmeters Transmitter types MAG 5000, MAG 6000 Operating Manual Edition 05/2006 - Revision 05 s *083R9175* Technical Documentation (handbooks, instructions, manuals etc.) on the complete product range SITRANS F can be found on the internet/intranet on the following links. SITRANS F M MAGFLO® Electromagnetic flowmeters Transmitter types MAG 5000, MAG 6000 Operating Manual Edition 05/2006 - Revision 05 s *083R9175* Technical Documentation (handbooks, instructions, manuals etc.) on the complete product range SITRANS F can be found on the internet/intranet on the following links.
INSTRUCTIONS
SITRANS F M MAGFLO
Electromagnetic flowmeter
type MAG 5100 W
ENGLISH
083R9166
SFIDK.PI.026.V1.52
Siemens Flow Instruments SITRANS F M MAGFLO
electromagnetic flowmeters consist of a
sensor and a transmitter. These instructions only describe the sensor installation. For further
information on the transmitter installation, please refer to the SITRANS F M MAGFLO
handbook.
Introduction
MAG 5100 W, compact/separate
Dimensions and
weight
mm
inch
mm
inch
mm
inch
mm
inch
mm
inch
mm
inch
mm
inch
25
1'
187
7.4
N/A
N/A
N/A
N/A
200
7.9
200
7.9
N/A
N/A
40
1½”
197
7.8
N/A
N/A
N/A
N/A
200
7.9
200
7.9
N/A
N/A
50
2'
188
7.4
N/A
N/A
200
7.9
N/A
N/A
200
7.9
N/A
N/A
65
2½”
194
7.6
N/A
N/A
200
7.9
N/A
N/A
200
7.9
N/A
N/A
80
3'
200
7.9
N/A
N/A
200
7.9
N/A
N/A
200
7.9
N/A
N/A
100
4'
207
8.1
N/A
N/A
250
9.8
N/A
N/A
250
9.8
N/A
N/A
125
5'
217
8.5
N/A
N/A
250
9.8
N/A
N/A
250
9.8
N/A
N/A
150
6'
232
9.1
N/A
N/A
300
11.8
N/A
N/A
300
11.8
N/A
N/A
200
8'
257
10.1
350
13.8
350
13.8
N/A
N/A
350
13.8
N/A
N/A
250
10'
284
11.2
450
17.7
450
17.7
N/A
N/A
450
17.7
N/A
N/A
300
12'
310
12.2
500
19.7
500
19.7
N/A
N/A
500
19.7
Manual Sitrans Fm Magflo Mag 5000 Series
N/A
N/A
350
14'
362
14.3
550
21.7
550
21.7
N/A
N/A
550
21.7
N/A
N/A
400
16'
387
15.2
600
23.6
600

23.6
N/A
N/A
600
23.6
N/A
N/A
450
18'
418
16.5
600
23.6
600
23.6
N/A
N/A
600
23.6
N/A
N/A
500
20'
443
17.4
625
24.6
625
24.6
N/A
N/A
680
26.8
N/A
N/A
600
24'
494
19.4
750
29.5
750
29.5
N/A
N/A
820
32.3
N/A
N/A
700
28'
544
21.4
875
34.4
875
34.4
N/A
N/A
N/A
N/A
875
34.4
750
30'
571
22.5
N/A
N/A
N/A
N/A
N/A
N/A
N/A
N/A
937
36.9
800
32'
606
23.9
1000
39.4
1000
39.4
N/A
N/A
N/A
N/A
1000
39.4
900
36'
653
25.7
1125
44.3
1125
44.3
N/A
N/A
N/A
N/A
1125
44.3
1000 40'
704
27.7
1250
49.2
1250
49.2
N/A
N/A
N/A
N/A
1250
49.2
42'
704
27.7
N/A
N/A
N/A
N/A
N/A
N/A
N/A
N/A
1250
49.2
1100 44'
755
Mag 5000 Flow Meter
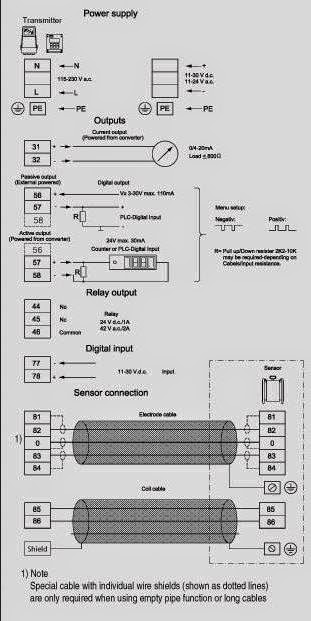
29.7
N/A
N/A
N/A
N/A
N/A
N/A
N/A
N/A
Manual Sitrans Fm Magflo Mag 5000 For Sale
1375
54.1
1200 48'
810
31.9
1500
59.1
1500
59.1
N/A
N/A

N/A
N/A
1500
59.1
AWWA
Nominal
size
A
L
PN 10
PN 16
PN 40
Class 150
Dimensions
s
Order no.: FDK:521H1190
Operating Manual
SITRANS F M MAGFLO® Electromagnetic flowmeters Transmitter type MAG 6000 19' & safety barrier [EEx ia/ib] IIB sensor type MAG 1100 Ex & MAG 3100 Ex
[
]
Order no.: FDK:521H1184 SFIDK.PS.026.C2.02
*083R9171*
ENGLISH
SITRANS F M MAGFLO ®
Contents
2
1.
Introduction ...................................................................................................................... 3
2. 2.1 2.2 2.3.1 2.3.2 2.4 2.5 2.6 2.7 2.8
Installation ....................................................................................................................... 4 Installation of transmitter MAG 6000 ............................................................................... 4 Installation of sensor ....................................................................................................... 4 Remote installation - At the sensor ................................................................................. 6 Remote installation - Transmitter in 19' insert ................................................................ 6 Ex survey according to Directive 94/9/EC (ATEX) .......................................................... 7 Overview and intrinsically safe data ............................................................................... 8 Device identification ........................................................................................................ 8 Approvals ........................................................................................................................ 9 Special conditions for safe use ..................................................................................... 10
3. 3.1.1 3.1.2 3.1.3 3.1.4 3.2
Electrical connection ..................................................................................................... 11 19” IP 20 version EEx (ia/ib) DN ≤ 300 ......................................................................... 11 19” IP 20 version EEx e (ib) DN ≥ 350 .......................................................................... 11 19” IP 66 version EEx (ia/ib) DN ≤ 300 ......................................................................... 11 19” IP 66 version EEx e (ib) DN ≥ 350 .......................................................................... 11 Transmitter MAG 6000 .................................................................................................. 12
4. 4.1.1 4.1.2 4.2.1 4.2.2 4.3 4.4.1 4.4.2 4.4.3 4.5
Technical data ............................................................................................................... 13 Dimensions and weight MAG 1100 Ex ......................................................................... 13 Sensor MAG 1100 Ex .................................................................................................... 14 Dimensions and weight MAG 3100 Ex ......................................................................... 15 Sensor MAG 3100 Ex .................................................................................................... 16 Transmitter MAG 6000 .................................................................................................. 17 Safety barrier (ia/ib) DN ≤ 300 ...................................................................................... 18 Safety barrier (ia) DN ≥ 350 .......................................................................................... 18 IS data sensor ............................................................................................................... 18 Output characteristics MAG 6000 ................................................................................. 19
5. 5.1 5.2.1 5.2.2 5.2.3 5.2.4 5.2.5 5.2.6
Commissioning ............................................................................................................. 20 Keypad and display layout ............................................................................................ 20 Basic settings ................................................................................................................ 21 Outputs .......................................................................................................................... 22 External input ................................................................................................................ 22 Sensor characteristics ................................................................................................... 23 Language mode ............................................................................................................ 23 Service mode ................................................................................................................ 24
6. 6.1 6.2
Service .......................................................................................................................... 25 Transmitter check list ..................................................................................................... 25 Trouble shooting MAG transmitter ................................................................................ 26
7.
Ordering ........................................................................................................................ 27
8. 8.1 8.2
Certificates .................................................................................................................... 28 EC-declaration of conformity ......................................................................................... 28 EC type examination certificate .................................................................................... 29
SFIDK.PS.026.C2.02
1.
Introduction
1.
Introduction
For safety reasons it is important that the following points, especially the points marked with a warning sign, are read and understood before the system is being installed: •
Installation, connection, commissioning and service must be carried out by personnel who are qualified and authorized to do so.
•
It is very important that the same people have read and understand the instructions and directions provided in this manual and that they follow the instructions and directions before taking the equipment into use!
•
People who are authorized and trained by the owner of the equipment may operate the equipment.
•
The installation must ensure that the measuring system is correctly connected and is in accordance with the connection diagram. The transmitter has to be earthed unless the power supply is galvanically isolated.
•
In applications with working pressures/media that can be dangerous to people, surroundings, equipment or others in case of pipe fracture, we recommend that special precautions such as special placement, shielding or installation of a security guard or a security valve should be made when the sensor is being installed.
•
Siemens Flow Instruments want to assist by estimating the chemical resistance of the sensor parts that are in connection with the media, but it is at any time the customer’s responsibility, which materials are chosen and Siemens Flow Instruments takes no responsibility if the sensor corrodes!
•
Equipment used in hazardous areas must be Ex-approved and marked for Europe and UL for USA. It is required that the special directions provided in the manual and in the Ex certificate must be followed!
•
Installation of the equipment must comply with national regulations. Example EN 60079-14 for Denmark.
•
Repair and service can be done by approved Siemens Flow Instruments personnel only.
SFIDK.PS.026.C2.02
3
ENGLISH
SITRANS F M MAGFLO ®
ENGLISH
SITRANS F M MAGFLO ®
2.
2. Installation
Installation
Transmitter MAG 6000 can be installed in the safe area only!
2.1 Installation of transmitter MAG 6000
Safe area only!
Category 2 equipment Sensors may be installed in zone 1 and zone 2.
2.2 Installation of sensor
Hazardous area
The sensor must always be completely full with liquid.
Therefore avoid: • Installation at the highest point in the pipe system • Installation in vertical pipes with free outlet
For partially filled pipes or pipes with downward flow and free outlet the flowmeter should be located in a U-tube.
Installation in vertical pipes Recommended flow direction: upwards. This minimizes the effect on the measurement of any gas/air bubbles in the liquid.
4
SFIDK.PS.026.C2.02
2. Installation
2.2 Installation of sensor (continued)
Installation in horizontal pipes The sensor must be mounted as shown in the upper figure. Do not mount the sensor as shown in the lower figure. This will position the electrodes at the top where there is possibility for air bubbles and at the bottom where there is possibility for mud, sludge, sand etc. If using empty pipe detection the sensor can be tilted 45°, as shown in the upper figure.
Measuring abrasive liquids and liquids containing particles Recommended installation is in a vertical/inclined pipe to minimize the wear and deposits in the sensor.
Inlet and outlet conditions To achieve accurate flow measurement it is essential to have straight lengths of inlet and outlet pipes and a certain distance between pumps and valves. It is also important to centre the flowmeter in relation to pipe flanges and gaskets.
Installation in large pipes The flowmeter can be installed between two reducers (e.g. DIN 28545). Assuming that at 8° the following pressure drop curve applies. The curves are applicable to water.
Example: A flow velocity of 3 m/s (V) in a sensor with a diameter reduction from DN 100 to DN 80 (d1/d2 = 0.8) gives a pressure drop of 2.9 mbar.
SFIDK.PS.026.C2.02
5
ENGLISH
SITRANS F M MAGFLO ®
ENGLISH
SITRANS F M MAGFLO ®
2. Installation
2.3.1 Remote installation At the sensor
Remove the SENSORPROM® unit from the sensor and mount it on the connection plate in the transmitter.
Fit and connect the electrode and coil cables as shown in chapter 7 “Electrical connections” in the handbook. The unscreened cable ends must be kept as short as possible. The electrode cable and the coil cable must be kept separate to prevent interference. Tighten the cable glands well to obtain optimum sealing. 2.3.2 Remote installation Transmitter in 19' insert
1. Fit the SENSORPROM® memory unit on the connection board supplied with the transmitter. The SENSORPROM® unit is supplied with the sensor in the terminal box. 2. Mount the guide rails into the rack system as shown. Distance between guide rails is 20 TE. Guide rails are supplied with the rack system and not with the transmitter. 3. Mount the connection board as shown. 4. Connect the cables as shown under 'Electrical connection', chapter 7 in the handbook. 5. Insert the transmitter into the rack system.
6
SFIDK.PS.026.C2.02
2. Installation II 2G E Ex ia IIB T3-T6 ENGLISH
as an example:
2.4 Ex survey according to Directive 94/9/EC (ATEX)
Instrument groups I
Applies to instruments used in underground mining operations, as well as their above ground operations, which can be endangered by mine gas and/or flammable dusts.
II
Applies to instruments used in the remaining areas which can be endangered by a potentially explosive atmosphere.
Directive 94/9/EC (ATEX)
Instrument category Labelling with gases Labelling with dusts
SITRANS F M MAGFLO ®
Definition
Instruments of this category are for use in areas where ignitable atmospheres, caused by 1G 1D a mixture of air and gasses, vapours or mists or (0) (20) by dust/air mixtures, can exist all of the time or for long periods of time or else frequently. 2G 2D (1) (21)
Instruments of this category are for use in areas where ignitable atmospheres caused, by a mixture of air and gasses, vapours or mists or by dust/air mixtures, can exist some of the time.
Instruments of this category are for use in areas where ignitable atmospheres, caused by 3G 3D a mixture of air and gasses, vapours or mists or (2) (22) by dust/air mixtures, are not likely to exist. However, if they do occur then in all probability, only seldom or for short periods of time. (The figures in brackets refer to IEC)
Built according to European norm = E Explosion protected electrial equipment = Ex Ex protection labelling in square brackets refers to 'Associated electrical equipment'
Type of protection o p q d e
Oil encapsulated i Pressurized apparatus n Powder filling m Flameproof enclosure s Increased safety
Intrinsic safety (ia, ib) Non-incentive equipment Encapsulation Special protection
Explosion groups
EN 50014
Gases and vapours (examples) • Ammonia • Acetone, aircraft fuel, benzine, crude oil, diesel oil, ethane, ethanoic acid, ether, gasolines, heating oil, hexane, methane, propane • Ethylene, isoprene, town gas • Acetylene, carbon disulphide, hydrogen
Minimum EN/ ignition IEC energy [mJ] IIA
0.18 0.06
IIA IIB
0.02
IIC
Ignition temperature Maximum surface temperature 450°C 842°F 300°C 572°F 200°C 392°F 135°C 275°F 100°C 212°F 85°C 185°F
SFIDK.PS.026.C2.02
EN / IEC T1 T2 T3 T4 T5 T6
7
ENGLISH
SITRANS F M MAGFLO ®
2. Installation
Specifications: Supply: 115-230 V or 24 V Ambient temperature: −20 to 50°C Enclosure: IP 20 or IP 65
2.5 Overview and intrinsically safe data
MAG 6000 19' IP 20 & IP 65 [EEx ia] IIB
IS data transmitter
Can only be installed in safe area! All MAG 1100 Ex and MAG 3100 Ex sensors have the following ratings and input parameters:
MAG 1100 & MAG 3100 EEx ia IIB T3...T6
Terminals MAG barriers Uo Io Po Lo Co
85-86 ib coil 28 V 138 mA 4 mH 100 nF
82-83 ia electrode 9.3 V 40 mA 0.4 W 23 mH 500 nF
Category 2 equipment Sensors may be installed in zone 1 and zone 2.
Sensors intrinsically safe data See table below.
IS data sensor MAG 1100 DN 6 - 100 MAG 3100 DN 15 - 300 Ex ib Terminals MAG sensor Ui Ii Pi Li Ci
2.6 Device identification
Sensor MAG 1100 Ex or MAG 3100 Ex label
8
SFIDK.PS.026.C2.02
85-86 coil 28 V 140 mA 2W 2 mH 50 nF
MAG 3100 DN 350 - 2000 Ex e ia 82-83 electrode 10 V 50 mA 0.5 W 20 mH 50 nF
Terminals MAG sensor Ui Ii Pi Li Ci
85-86 coil -
82-83 electrode 10 V 50 mA 0.5 W 20 mH 50 nF
SITRANS F M MAGFLO ®
2. Installation
2.7 Approvals
ENGLISH
Transmitter MAG 6000 19' IP 20 and IP 65 label
SITRANS F M MAGFLO® sensors carry the following approvals MAG 1100 Ex for mounting in Ex areas DN 6 - DN 100 EEx [ia] [ib] IIB T4...T6, II 2 (1)(2) SIRA 03 ATEX 1423X CE 0518
Temperature ratings are as follows: T4 (max. surface < 135°C) for liquid temperatures lower than 100°C T5 (max. surface < 100°C) for liquid temperatures lower than 82°C T6 (max. surface < 85°C) for liquid temperatures lower than 67°C For an ambient temperature of –20°C to + 50°C MAG 3100 Ex for mounting in Ex areas DN 15 - DN 300 EEx-d [ia] [ib] IIB T4...T6, II 2 (1)(2) SIRA 03 ATEX 1442X CE 0518
Temperature ratings are as follows*): T4 (max. surface < 135°C) for liquid temperatures lower than 100°C T5 (max. surface < 100°C) for liquid temperatures lower than 87°C T6 (max. surface < 85°C) for liquid temperatures lower than 72°C For an ambient temperature of –20°C to +50°C DN 350 - DN 2000 EEx e ia IIC T3…T6, II 2 GD IP 65 T(**) OC SIRA 03 ATEX 3339X CE 0518 where (**) represents the pipeline temperature + 5K for the purposes of the dust approval
Temperature ratings are as follows*): T3 (max. surface < 200°C) for liquid temperatures lower than 190°C T4 (max. surface < 135°C) for liquid temperatures lower than 125°C T5 (max. surface < 100°C) for liquid temperatures lower than 90°C T6 (max. surface < 85°C) for liquid temperatures lower than 75°C For an ambient temperature of –20°C to +40°C
MAG 6000 & safety barriers carry the following approvals For use with MAG 1100 Ex (all sizes) and MAG 3100 Ex sizes DN 15 - DN 300 for mounting in the safe area [EEx ia ib] IIB, II 2 G DEMKO 03 ATEX 135255X CE539 For use with MAG 3100 Ex sizes DN 350 - DN 2000, for mounting in the safe area [EEx ia] IIC, II 2 G DEMKO 03 ATEX 135254X CE539 *) Note Temperature ratings may be limited by the lining selected, see section 4.2.2.
SFIDK.PS.026.C2.02
9
ENGLISH
SITRANS F M MAGFLO ®
2. Installation
2.8 Special conditions for safe use
MAG 3100 Ex DN 40 - DN 300 The relation between assigned temperature ambient temperature and media temperature: Temperature class T6 T5 T4
Ambient temperature range −20 °C to +50 °C −20 °C to +50 °C −20 °C to +50 °C
Media temperature range −20 °C to +60 °C −20 °C to +75 °C −20 °C to +100 °C
This electrode circuit 'ia' is connected to the media inside the sensor. The screen for the 'ib' circuit is connected to chassis and the installations shall therefore take that into account. Safety Barrier type FDK:083F50_ _ for MAG sensors
Special conditions for safe use:
10
•
The ambient temperature range is −20 °C to +50 °C.
•
The safety barrier shall be connected to the PE earth (light blue) according to local installation equipments. IEC 60079-14 can be used as guideline.
•
The PE earth shall be connected to the PE at the sensor according to local installation equipments. IEC 60079-14 can be used as guideline.
•
The intrinsic safety wiring shall be separated from non intrinsic safety wiring according to local installation equipments.
•
The apparatus must be installed in plastic enclosure code FDK:083F5038 with an Ingress Protection suitable for the environment. The plastic box FDK:083F5038 has been evaluated for IP 65 according to EN 60529: 1989.
SFIDK.PS.026.C2.02
SITRANS F M MAGFLO ®
Electrical connection
ENGLISH
3.
3. Electrical connection
3.1.1 19” IP 20 version EEx (ia/ib) DN ≤ 300
3.1.2 19” IP 20 version EEx e (ib) DN ≥ 350
3.1.3 19” IP 66 version EEx (ia/ib) DN ≤ 300
3.1.4 19” IP 66 version EEx e (ib) DN ≥ 350
1. Connection terminals to: • Power supply • In- and output 2. Connection terminals to: Sensors Intrinsically safe terminals! It is an absolute requirement that the wires/terminals of the intrinsically safe circuits cannot get into contact with the wires of the other cables. The distance between cables/wires therefore must be at least 50 mm. It is recommended to fasten the cables/wires in a way that they, even in case of an error, cannot get into contact with each other. Make the wire ends as short as possible. SFIDK.PS.026.C2.02
11
ENGLISH
SITRANS F M MAGFLO ®
3. Electrical connection
3.2 Transmitter MAG 6000
Installation
1) Mains supply 115 to 230 V AC from building installation Class II. A switch or circuitbreaker (max. 15 A) shall be included in the building installation. It must be in close proximity to the equipment and within easy reach of the OPERATOR, and it shall be marked as the disconnecting device for the equipment. 2) Protective conductor terminal. Required cable min. AGW16 or 1.5 Cu. The insulation between the connected mains supply and 24 V AC/DC supply for the flowmeters, models 24 V AC/DC shall at least be rated with double or reinforced insulation at mains voltage. For field wiring installation National Installation Code shall be met of the country, where the flowmeters are installed. Digital output If the internal resistance of the loads exceeds 10KΩ, it is recommended to connect an external 10KΩ load resistor in parallel to the load.
12
SFIDK.PS.026.C2.02
4. Technical data
4.
MAG 1100/6000 and MAG 1100/5000, compact/separate
Technical data
ENGLISH
SITRANS F M MAGFLO ®
4.1.1 Dimensions and weight MAG 1100 Ex
1) 2)
DN
A1)
B1)
A1
B1
D
6 10 15 25 40 50 65 80 100
[mm] 161 161 161 169 181 189 199 205 218
[mm] 186 186 186 201 223 240 259 271 297
[mm] 314 314 314 322 334 342 352 358 371
[mm] 339 339 339 354 376 393 412 424 450
[mm] 48.3 48.3 48.3 63.4 84.0 101.6 120.0 133.0 159.0
Di Di Ceramic (PFA) [mm] [mm] 6 10 10 15 16 25 26 40 38 50 50 65 66 80 81 100 100
Dp
DG
Weight 2)
[mm] 17.3 17.3 17.3 28.5 43.4 54.5 62.5 82.5 107.1
[mm] 34 34 40 56 75 90 112 124 150
[kg] 2.2 2.2 2.2 2.7 3.4 4.2 5.5 7.0 10.0
13 mm shorter when the AISI terminal box is used (high temperature 200 °C). With transmitter MAG 5000 or MAG 6000 installed, weight is increased by approx. 0.8 kg.
SFIDK.PS.026.C2.02
13
ENGLISH
SITRANS F M MAGFLO ® 4.1.2 Sensor MAG 1100 Ex
4. Technical data
Type Nominal size Operating pressure
mm
Temperature of medium Ceramic Temperature shock (Ceramic liner)
Ambient temperature Liner Electrodes Enclosure Terminal box Fixing studs Mating flanges Gaskets
Cable entries Enclosure rating
Standard Option Option Standard Option
Mechanical load (vibration) Test pressure Approvals Excitation frequency Conforms to PED, LVT, EMC
14
SFIDK.PS.026.C2.02
Flangeless sensor (Sandwich design) DN 6, 10, 15, 25, 40, 50, 65, 80, 100 DN 6 - DN 65: 40 bar, DN 80: 37.5 bar, DN 100: 30 bar Vacuum: 1 × 10-6 bar −20°C to +120°C (Duration > 1 min.): DN 6, 10, 15, 25: Max. ∆T ≤ 15°C/min. DN 40, 50, 65: Max. ∆T ≤ 10°C/min. DN 80, 100: Max. ∆T ≤ 5°C/min. (Duration ≤ 1 min., followed by 10 min. rest): DN 6, 10, 15, 25: Max. ∆T ≤ 80°C DN 40, 50, 65: Max. ∆T ≤ 70°C DN 80, 100: Max. ∆T ≤ 60°C Remote transmitter: −40°C to +100°C Aluminium oxide Al2O3 (ceramics) Platinum with gold/titanium brazing alloy Stainless steel AISI 316 L (1.4404) Stainless steel AISI 316 (1.4436) Stainless steel AISI 304 (1.4301) Number and size to EN 1092-1:2001 EN 1092-1:2001, ANSI B16.5 class 150 and 300 or equivalent EPDM (max. 150°C, PN 40) Graphite (max. 200°C, PN 40) PTFE (max. 130°C, PN 25) 4 Pg 13.5 IP 67 to EN 60529 (NEMA 4x) (1 m w.g for 30 min.) IP 68 to EN 60529 (NEMA 6) (10 m w.g. cont.) 18-1000 Hz random in all directions to EN 60068-2-36 Sensor: 3.17 G/Compact Ex-d: 1.14 G 80 bar (2 × PN) See section 2.7 DN 6 - 65: 6.25 Hz DN 80 - 100: 3.125 Hz PED - 97/23EC, LVD - 73/23 EEC + amendment 93/68/EEC, EMC - 89/336 EEX
4. Technical data
4.2.1 Dimensions and weight MAG 3100 Ex
MAG 3100 Ex
A1
B
L 2)
D1 EN 1092-1-2001 PN 6, 10
[mm] 15 25 40 50 65 80 100 125 150 200 250 300 350 400 450 500 600 700 750 800 900 1000 1100 1200 1400 1500 1600 1800 2000 1) 2) 3) 4)
PN 16
PN 25
[mm] [mm] [mm] [mm] [mm] [mm] [mm] 199 338 59 104 200 200 200 199 338 59 104 200 200 200 209 348 82 124 200 200 200 217 356 72 139 200 200 200 224 363 72 154 200 200 200 234 373 72 174 200 200 272 254 393 85 214 250 250 250 267 406 85 239 250 250 250 288 427 85 282 300 300 300 316 455 137 338 350 350 350 344 483 137 393 450 450 450 369 508 137 444 500 500 500 362 513 270 462 550 550 550 387 538 270 512 600 600 600 418 569 310 563 600 600 600 443 594 350 614 625 625 625 494 645 430 715 750 750 750 544 695 500 816 875 875 571 722 556 869 606 757 560 939 1000 1000 653 804 630 1042 1125 1125 704 906 670 1146 1250 1250 755 906 770 1248 1375 1375 810 961 792 1348 1500 1500 925 1076 1000 1675 1750 1750 972 1123 1020 1672 1025 1176 1130 1915 2000 2000 1123 1274 1250 1974 2250 2250 1223 1374 1375 2174 2500 2500 -
PN 40
PN 64
PN 100
AS TC 3) TE 3) 2129 E, AWWA AS 4087 C-207 Class Class 14-21D 35 [mm] [mm] [mm] [mm] [mm] 200 200 6 200 200 1.2 6 270 200 1.2 6 270 200 1.2 6 280 200 1.2 6 290 200 1.2 6 310 250 1.2 6 335 250 1.2 6 300 300 1.2 6 350 350 1.2 8 450 450 1.2 8 500 500 1.6 8 550 550 1.6 8 600 600 1.6 10 640 600 1.6 10 730 625 1.6 10 860 750 1.6 10 875 875 2.0 937 937 2.0 1000 1000 2.0 1125 1125 2.0 1250 1250 2.0 2.0 1500 1500 2.0 3.0 1875 1875 3.0 3.0 3.0 3.0 -
BS 1560/ ANSI 16.5 Class Class 150 300
[mm] [mm] [mm] [mm] 200 200 200 260 200 200 280 270 200 276 300 270 200 320 350 280 272 323 340 290 250 380 400 250 250 420 450 250 300 415 450 300 350 480 530 350 450 550 620 450 500 600 680 500 550 700 800 550 600 750 600 600 600 680 680 750 820 -
4)
A1)
Weight
DN
ENGLISH
SITRANS F M MAGFLO ®
[kg] 4 5 8 9 11 12 16 19 27 40 60 80 110 125 175 200 300 350 380 475 560 700 1200 1250 1753 2600 2341 3253 4060
13 mm shorter with AISI terminal box (Ex and high temperature) When earthing flanges are used, the thickness of the earthing flange must be added to the built-in length TC = Type C grounding ring, TE = Type E grounding ring Weights are approx. and for PN 16 without transmitter
D = Outside diameter of flange, see flange tables
SFIDK.PS.026.C2.02
15
ENGLISH
SITRANS F M MAGFLO ®
4.2.2 Sensor MAG 3100 Ex
4. Technical data
Type Nominal size mm Temperature of medium1) Liner: Neoprene (standard) EPDM2) Linatex® rubber Ebonite 2) PTFE Ambient temperature Operating pressure3) [abs.bar]] Liner: Neoprene EPDM Linatex® Ebonite PTFE teflon: DN 15 to 600: Excitation frequency
Enclosure rating
Standard Option
Cable entries Mechanical load Test pressure Flanges Standard EN 1092-1:20014) Rased face
Option
ANSI B 16.5 (∼BS 1560) AS 2129 AS 4087
AWWA C-207 Electrodes
PE - electrodes Measuring pipe Flange and housing material
Standard Option Standard Standard Option Standard Option
Option Ex-approval Conforms to PED, LVT, EMC
0.01 0.01 0.01 0.01
T6 0 to 70°C −10-75°C −20 to 70°C 0 to 75°C −20 to 75°C
to 100 bar to 40 bar to 40 bar to 100 bar
0.3 to 40 bar DN 15 - 65: 6.25 Hz DN 80/100: 3.125 Hz DN 125 - 300: 1.5625 Hz DN 350 - 1200: 3.125 Hz IP 67 to EN 60529 (NEMA 4x) (1 m w.g for 30 min.) IP 68 to EN 60529 (NEMA 6) (10 m w.g. cont.) 4 Pg 13.5 18-1000 Hz random, 3.17 G rms in all directions to EN 60068-2-36 1.5 × PN DN 15-50: PN 40 DN 65-150: PN 16 DN 200-1000: PN 10 DN 1100 -2000: PN 6 DN 65-1000: PN 6 DN 1200-2000: PN 10 DN 200-2000: PN 16 DN 200-600: PN 25 DN 65-600: PN 40 DN 50-400 PN 63 DN 25-350 PN 100 3/4'-24': Class 150 (20 bar) 3/4'-24': Class 300 (50 bar) 3/4'-48': Table D/E Class 14 (DN 50 - 1200, 14 bar) Class 21 (DN 50 - 600, 21 bar) Class 35 (DN 50 - 600, 35 bar) 28'-78': Class D (10 bar) AISI 316 Ti (1.4571) Hastelloy C-276, Platinum / Iridium, Titanium, AISI 316 Ti Ceramic Coated, Tantalum As measuring electrodes (except PTFE) AISI 304 (1.4301) AISI 316 L (1.4404) Carbon steel Corrosion-resistant two-component coating (min. 150 µm) AISI 304 (1.4301) flanges and carbon steel housing. Coating as above AISI 316 L (1.4404) flanges and housing See section 2.7 PED - 97/23EC, LVD - 73/23 EEC + amendment 93/68/EEC, EMC - 89/336 EEX
1)
The maximum fluid temperature may be further limited by the approval temperature ratings, see section 2.7
2)
With WRC (Water Research Council, UK) approval
3)
Maximum operating pressure decreases with increasing operating temperature and with stainless steel flanges
4)
16
Sensor with flanges DN 15 - DN 2000 Temperature classification T3 + T4 T5 0 to 70°C 0 to 70°C −10 to 95°C −10 to 90°C −20 to 70°C −20 to 70°C 0 to 95°C 0 to 90°C −20 to 100°C −20 to 90°C Remote transmitter: −20°C to 50°C
EN 1092-1, DIN 2501 & BS 4504 have the same mating dimensions
SFIDK.PS.026.C2.02
4.3 Transmitter MAG 6000 Accuracy 0.25%
4. Technical data
Current output Current Load Time constant Digital output Frequency Time constant Active Passive Relay Time constant Load Digital input Activation time Current Functions
ENGLISH
SITRANS F M MAGFLO ®
0-20 mA, 4-20 mA or 4-20 mA + alarm < 800 ohm 0.1-30 s adjustable 0-10 kHz, 50% duty cycle 0.1-30 s adjustable 24 V DC, 30 mA, 1 KΩ ≤ Rload ≤ 10 KΩ, short-circuit-protected 3-30 V DC, max. 110 mA, 200 Ω ≤ Rload ≤ 10 KΩ Changeover relay, time constant same as current time constant 42 V AC/2 A, 24 V DC/1A 11-30 V DC, Ri = 4.4 KΩ 50 ms I11 V DC = 2.5 mA, I30 V DC = 7 mA Flow rate, 2 totalizers, low flow cut-off, empty pipe cut-off, flow direction, error system, operating time, uni/bidirectional flow, limit switches, pulse output, control for cleaning unit and batch All inputs and outputs are galvanically isolated
Galvanic isolation Cut-off Low flow Empty pipe Totalizer Display
Time constant Zero point adjustment Electrode input impedance Excitation frequency Ambient temperature
Custody transfer approval MAG 6000 CT
0-9.9% of maximum flow Detection of empty pipe1) Two eight-digit counters for forward, net or reverse flow Background illumination with alphanumerical text, 3 × 20 characters to indicate flow rate, totalized values, settings and faults Reverse flow indicated by negative sign Time constant as current output time constant Automatic > 1 x 1014 Ω Sensor size depending pulsating DC current (125 mA) Display version during operation: −20 to +50°C Blind version during operation: −20 to +60°C During storage: −40 to +70°C (RH max. 95%) PTB DANAK OIML R75 DANAK OIML R117 (cold water) (hot water) (cold water/milk, beer etc.) 6.221 99.19
Communication
Standard Optional 19' insert Enclosure material
Enclosure rating Mechanical load EMC performance Supply voltage Power consumption
1)
Prepared for client mounted add-on modules HART, Profibus PA as add-on module Standard 19' insert of aluminium/steel (DIN 41494) Width: 21 TE Height: 3 HE IP 20 to EN 60529 and DIN 40050 Version: 1 G, 1-800 Hz sinusoidal in all directions to EN 60068-2-36 Emission: EN 50081-1 (Light industry) Immunity: EN 50082-2 (Industry) 115-230 V AC +10% to −15%, 50-60 Hz 11-30 V DC or 11-24 V AC 230 V AC: 17 VA 24 V DC: 9 W, IN = 380 mA, IST = 8A (30 ms) 12 V DC: 11 W, IN = 920 mA, IST = 4A (250 ms)
Special cable required in separate mounted installation
SFIDK.PS.026.C2.02
17
ENGLISH
SITRANS F M MAGFLO ®
4.4.1 Safety barrier (ia/ib) DN ≤ 300
4. Technical data
Application Ex approval Ambient temperature 19' insert Enclosure material
As combined unit with MAG 6000 only and MAG 1100 Ex/3100 Ex in the size range DN 6-300 See section 2.7 During operation: −20 to +50°C During storage: −20 to +70°C Standard 19' insert in aluminium/steel (DIN 41494) Width: 21 TE Height: 3 HE IP 20 to EN 60529 and DIN 40050 1 G, 1-800 Hz sinusoidal in all directions to EN 60068-2-36
Enclosure rating Mechanical load EMC performance Emission Immunity
EN 50081-1 (Light industry) EN 50082-2 (Industry)
IS data transmitter Terminals MAG barriers Uo Io Po Lo Co
4.4.2 Safety barrier (ia) DN ≥ 350
85-86 ib coil 28 V 138 mA 4 mH 100 nF
Application Ex approval Ambient temperature 19' insert Enclosure material
Enclosure rating Mechanical load EMC performance Emission Immunity
82-83 ia electrode 9.3 V 40 mA 0.4 W 23 mH 500 nF
For use with MAG 5000/6000 19 insert and MAG 3100 Ex in the size range DN 350-2000 See section 2.7 During operation: −20 to +50°C During storage: −20 to +70°C Standard 19' insert in aluminium/steel (DIN 41494) Width: 21 TE Height: 3 HE IP 20 to EN 60529 and DIN 40050 1 G, 1-800 Hz sinusoidal in all directions to EN 60068-2-36 EN 50081-1 (Light industry) EN 50082-2 (Industry)
IS data transmitter Terminals MAG barriers Uo Io Po Lo Co
4.4.3 IS data sensor
MAG 1100 DN 6 - 100 MAG 3100 DN 15 - 300 Ex ib Terminals MAG sensor Ui Ii Pi Li Ci
18
82-83 ia electrode 9.3 V 40 mA 0.4 W 23 mH 500 nF
SFIDK.PS.026.C2.02
85-86 coil 28 V 140 mA 2W 2 mH 50 nF
MAG 3100 DN 350 - 2000 Ex e ia 82-83 electrode 10 V 50 mA 0.5 W 20 mH 50 nF
Terminals MAG sensor Ui Ii Pi Li Ci
85-86 coil -
82-83 electrode 10 V 50 mA 0.5 W 20 mH 50 nF
4.5
Output characteristics MAG 6000
4. Technical data
Output characteristics 0-20 mA
Bidirectional mode
Unidirectional mode
ENGLISH
SITRANS F M MAGFLO ®
4-20 mA
Frequency
Pulse output
Relay Power down
Active
Error relay
No error
Error
Limit switch or direction switch
1 set point
2 set points
Low flow (Reverse flow) High flow (Forward flow)
Intermediate flow
Hold
Batch
High flow/ Low flow
Batch on digital output (MAG 6000 only)
Batch on relay (MAG 6000 only)
SFIDK.PS.026.C2.02
19
ENGLISH
SITRANS F M MAGFLO ®
5.
5. Commissioning
Commissioning
5.1 Keypad and display layout
Keypad
Display
The keypad is used to set the flowmeter. The function of the keys is as follows: TOP UP KEY
This key (hold 2 sec.) is used to switch between operator menu and setup menu. In the transmitter setup menu, a short press will cause a return to the previous menu.
FORWARD KEY
This key is used to step forward through the menus. It is the only key normally used by the operator.
BACKWARD KEY
This key is used to step backward through the menus.
CHANGE KEY
This key changes the settings or numerical values.
SELECT KEY
This key selects the figures to be changed.
LOCK/UNLOCK KEY
This key allows the operator to change settings and gives access to submenus.
The display is alphanumerical and indicates flow values, flowmeter settings and error messages. The upper line is for primary flow readings and will always show either flow rate, totalizer 1 or totalizer 2. The line is divided into 3 fields. S: Sign field P: Primary field for numerical value U: Unit field The centre line is the title line (T) with individual information according to the selected operator or setup menu. The lowest line is the subtitle line (ST) which either will add information to the title line or keep individual information independent of the title line. F: The alarm field.
Two flashing triangles will appear by a fault condition.
M: The mode field. The symbols indicate the following.
L:
20
Communication mode
Basic settings
Operator active
Service mode
Output
Operator inactive
Operator menu
External input
Product identity
Sensor characteristics
Language mode
Reset mode
The lock field. Indicates the function of the lock key. Ready for change
Access to submenu
Value locked
RESET MODE: Zero setting of totalizers and initialization of setting
SFIDK.PS.026.C2.02
5. Commissioning
5.2.1 Basic settings
Main frequency To select the main power supply frequency corresponding to the country in which the flowmeter is installed. (US = 60 Hz) Flow direction Select the correct flow direction in the pipe. Qmax. Sets the measuring range, the analog outputs and the frequency output. Value, decimal point, unit and time can be set individually (setting is dimension dependent). Qmax.2 Sets the measuring range, the analog outputs and the frequency output. Value, decimal point, unit and time can be set individually (setting is dimension dependent). Only visible when it has been choosen as external digital input. Totalizers To set unit and decimal point. Low flow cutt off To set a % of selected Qmax.. To filter noise in the installation. Influences display and all outputs. Error level To select which error level, the flowmeter will detects an error.
Comma for flow rate, totalizer 1 and totalizer 2 can be individually positioned. • open the respective window. • ensure that the cursor is positioned below the comma. Use the SELECT KEY • move the comma to the requested position. Use the CHANGE KEY .
.
Units are changed by means of the CHANGE KEY with the cursor placed below the unit selected. Select units (cursor moved) by means of the SELECT KEY . Totalizer 2 is not visible when batch is selected as digital output. Qmax. 2 - is only visible when it has been choosen as external input. SFIDK.PS.026.C2.02
21
ENGLISH
SITRANS F M MAGFLO ®
ENGLISH
SITRANS F M MAGFLO ®
5. Commissioning
5.2.2 Outputs
Current output Proportional to flowrate (Terminal 31 and 32) 4 - 20 mA + alarm: Current output gives the following mA, depending on what is selected as error level in basic settings. Fatal: 1 mA, permanent: 2 mA, warning: 3 mA
The current output must be set off when not used.
Digital output Pulse/volume (Terminal 56, 57, 58)
Digital output Frequency Proportional to flowrate (Terminal 56, 57, 58)
5.2.3 External input
Batch control is available on MAG 6000 only.
22
SFIDK.PS.026.C2.02
SITRANS F M MAGFLO ®
5. Commissioning
ENGLISH
5.2.4 Sensor characteristics
If “SENSORPROM not installed” is shown, refer to chapter 6 in the handbook (depending on type of mounting configuration).
5.2.5 Language mode
SFIDK.PS.026.C2.02
23
ENGLISH
SITRANS F M MAGFLO ®
5. Commissioning
5.2.6 Service mode
1) Standard 2) If digital output is set to frequency
All previous settings are reinitialised when service mode is exited using the top up key. The error system The error system is divided into an error pending list and a status log list. Time is gained as days, minutes and hours since the error has occurred. The first 9 standing errors are stored in error pending. When an error is removed it is removed from error pending. The latest 9 errors are stored in the status log. When an error is removed it is still kept in status log. Errors in status log is stored for 180 days. Error pending and status log are accessible when enabled in the operator menu. 24
SFIDK.PS.026.C2.02
6. Service
6.
Often problems with unstable/wrong measurements occur due to insufficient/wrong earthing or potential equalization. Please check this connection. If OK, the SITRANS F M MAGFLO® transmitter can be checked as described under 9.1 and sensor under 9.3 in the handbook.
Service
When checking SITRANS F M MAGFLO® installations for malfunction the easiest method to check the transmitter is to replace it with another MAG 5000/6000 transmitter with a similar power supply. A replacement can easily be done as all settings are stored in and downloaded from the SENSORPROM® unit - no extra settings need to be made.
6.1 Transmitter check list
If no spare transmitter is available - then check transmitter according to check table.
Power on transmitter, display light on
YES
YES Error triangles flashing
NO
NO
Check cables/connections YES Check connection board Check pins in transmitter multiplug - OK
YES Output readings OK
NO
NO
Correct fault
Check error table
Display defect Change display
transmitter defective
Output and display readings OK ?
YES
NO Check cables/connections YES Check connection board Check pins in transmitter multiplug - OK
Transmitter OK Check settings/application Check installation/sensor/ earthing connection etc.
NO Correct fault
SFIDK.PS.026.C2.02
25
ENGLISH
SITRANS F M MAGFLO ®
ENGLISH
SITRANS F M MAGFLO ®
6.2 Trouble shooting MAG transmitter
6. Service
Symptom Empty display
Output signals Minimum
No flow signal
Minimum
Error code
F70 W31
Undefined
F60 P42 P41
Indicates flow with no flow in pipe
Unstable flow signal
Measuring error
Undefined
P40 P44
F61 F62 F63 F71 W30 W21
Measuring approx. 50%
26
SFIDK.PS.026.C2.02
1. No power supply
Power supply Check MAG 5000/6000 for bended pins on the connector Replace MAG 5000/6000 Turn on current output Turn on digital output Change direction Check cables/connections Ensure that the measuring pipe is full Replace MAG 5000/6000 Check cables/connections Replace MAG 5000/6000 Switch off MAG 5000/6000, wait 5 s and switch on again Select empty pipe cut-off Ensure that the measuring pipe is full Ensure that electrode cable is connected and sufficiently screened Increase time constant Use special electrode cable
2. MAG 5000/6000 defective 1. Current output disabled 2. Digital output disabled 3. Reverse flow direction Incorrect or no coil current Measuring pipe empty Internal error 1. No load on current output 2. MAG 5000/6000 defective Initializing error
Electrode connection missing/ electrode cable is insufficiently screened 1. Pulsating flow 2. Conductivity of medium too low 3. Electrical noise potential between medium and sensor 4. Air bubbles in medium
Undefined
Loss of totalizer OK data ##### OK Signs in display
Remedy
Measuring pipe empty Empty pipe cut-off is OFF
Unstable
Maximum
Cause
W20
5. High concentration of particles or fibres Incorrect installation No SENSORPROM® unit CT SENSORPROM® unit
Deficient SENSORPROM® unit Wrong type of SENSORPROM® unit Deficient SENSORPROM® unit Loss of internal data Flow exceeds 100% of Qmax. Pulse overflow • Volume/pulse too small • Pulse width too large Missing one electrode connection Initializing error Totalizer roll over
Ensure sufficient potential equalization Ensure medium does not contain air bubbles Increase time constant Check installation Install SENSORPROM® unit Replace SENSORPROM® unit or reset SENSORPROM® unit with MAG CT transmitter Replace SENSORPROM® unit Replace SENSORPROM® unit Replace SENSORPROM® unit Replace MAG 5000/6000 Check Qmax. (Basic Settings) Change volume/pulse Change pulse width Check cables Reset totalizer manually Reset totalizer or increase totalizer unit
7. Ordering
7. Ordering
Please look on our homepage http://www.siemens.com/flow under 'Product Selector'.
SFIDK.PS.026.C2.02
ENGLISH
SITRANS F M MAGFLO ®
27
ENGLISH
SITRANS F M MAGFLO ®
8. Certificates
8.1 EC-declaration of conformity
Please note the following certificates are incomplete for the full version please refer to http:// siemens.com/flow
28
SFIDK.PS.026.C2.02
8. Certificates
8.2 EC type examination certificate
Please note the following certificates are incomplete for the full version please refer to http:// siemens.com/flow
SFIDK.PS.026.C2.02
29
ENGLISH
SITRANS F M MAGFLO ®
SITRANS F M MAGFLO ®
8. Certificates
ENGLISH
Appendix to certificate Number: Sira 03ATEX1442X.
30
SFIDK.PS.026.C2.02
SITRANS F M MAGFLO ®
8. Certificates
ENGLISH
Please note the following certificates are incomplete for the full version please refer to http://siemens.com/flow
SFIDK.PS.026.C2.02
31
SITRANS F M MAGFLO ®
8. Certificates
ENGLISH
Please note the following certificates are incomplete for the full version please refer to http://siemens.com/flow
32
SFIDK.PS.026.C2.02
SITRANS F M MAGFLO ®
8. Certificates
SFIDK.PS.026.C2.02
ENGLISH
Please note the following certificates are incomplete for the full version please refer to http://siemens.com/flow
33
ENGLISH
SITRANS F M MAGFLO ®
8. Certificates
Please note the following certificates are incomplete for the full version please refer to http://siemens.com/flow
34
SFIDK.PS.026.C2.02
ENGLISH
SITRANS F M MAGFLO ®
SFIDK.PS.026.C2.02
35
We have checked the contents of this manual for agreement with the hardware and software described. Since deviations cannot be precluded entirely, we cannot guarantee full agreement. However, the data in this manual are reviewed regularly and any necessary corrections included in subsequent editions. Suggestions for improvement are always welcomed.
The reproduction, transmission or use of this document or its contents is not permitted without express written authority. Offenders will be liable for damages. All rights, including rights created by patent grant or registration of a utility model or design, are reserved.
Technical data subject to change without prior notice.
Copyright © Siemens AG 06.2005 All Rights Reserved
Siemens Flow Instruments A/S Nordborgvej 81 DK-6430 Nordborg
Order no.: FDK:521H1184-02 Printed in: Denmark